Solutions
Reducing CO2 emissions through the use of plastic for automotive parts
Recently, fuel efficiency of automobiles is strongly required due to environmental problems (especially the rising voices of reducing carbon dioxide emissions). The use of plastic fuel tanks is increasing because they are lighter than steel tanks, and that is easy to make difficult shapes when the platform is becoming more and more complex due to changing into hybrid vehicles.
Although the performance required for polyethylene for fuel tanks are extremely strict in terms of impact resistance, durability, (low) fuel extraction, etc., we have achieved more than 10% weight reduction compared to 10 years ago by powerfully and continuously pushing the development of new concept resins. We will continue to provide eco-friendly products.
the reduction of environmental burdens.
Peripheral parts of the fuel tank are also turning into plastic. As changing filler pipes which transports fuel from the refueling port to the fuel tank can reduce weight by 40-50%compared to metal, the number of car models equipping these pipes are increasing.
For filler pipes, not only do they need the properties required for fuel tanks, but they also require electrical conductivity. We are working continuously to developing the best grade for filler pipes and will continue to provide our customers with it.
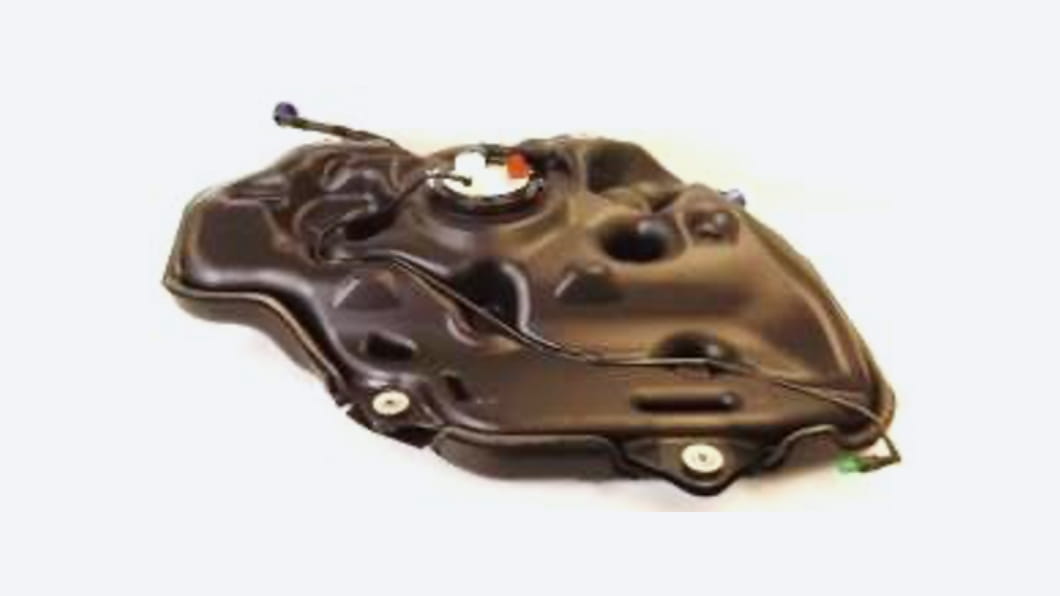
Photo Courtesy: FTS Inc.
(Car model "Prius™")
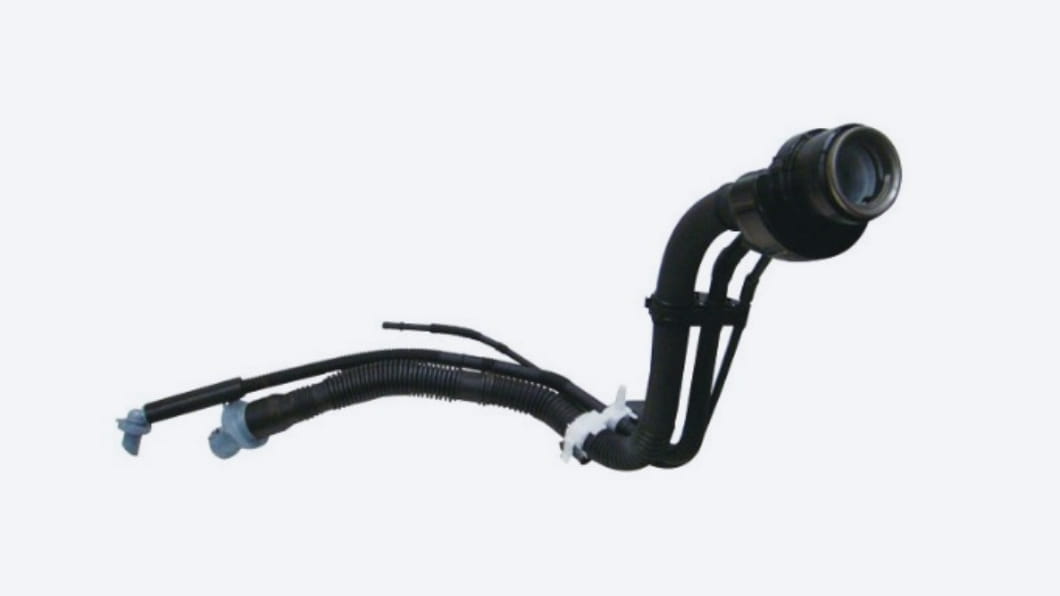
Photo Courtesy:Toyoda Gosei Co.
Developing products that contribute to the realization of a low-carbon society
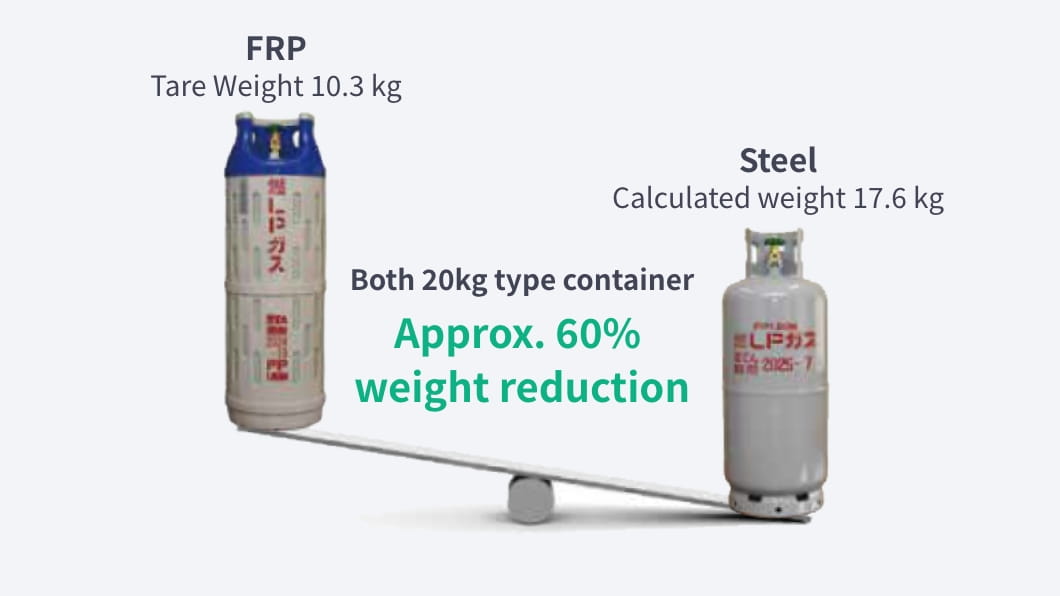
Photo Courtesy Chugoku Industrial Co.
Liquefied petroleum gas (LP gas) is positioned as an energy source that can contribute to the realization of a low-carbon society because it emits relatively little carbon dioxide when burned. However, its containers were conventionally made of steel, making it difficult to check and remaining gas volume. Also, the containers were so heavy to move. The development of composite containers made of resin and glass fiber made it possible to reduce the weight of the containers and the frequency of replacement by checking the remaining volume, thereby reducing the workload and contributing to the reduction of carbon dioxide emissions during transportation.
The use of LP gas composite containers is currently spreading, with the 7.5 kg type being launched in 2015 and the 20 kg type in 2020.
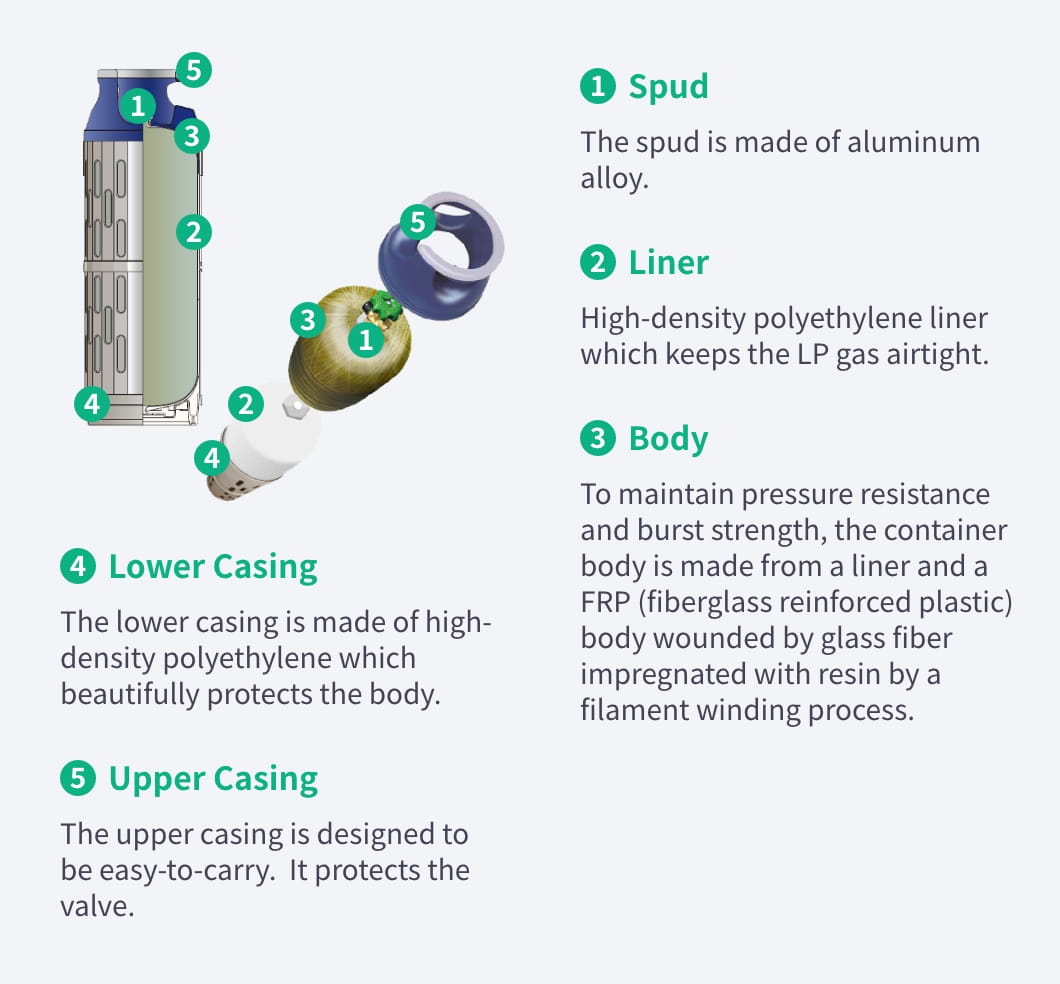
Photo Courtesy: Chugoku Industrial Co.
LP gas composite containers are consisted by a pressure vessel made of polyethylene liner wrapped with glass fiber and a polyethylene casing which protects the vessel. We have products suitable for liner components that require high durability to meet the required service life of the container and casing components that require high moldability to accommodate complex designs and high impact resistance to adequately protect the container. In Japan, Chugoku Industrial Co. is using our grades for their PLACOMPO™, an LP gas composite container.
We will continue to develop and provide products that contribute to the realization of a low-carbon society.
Developing products for environmentally friendly packaging
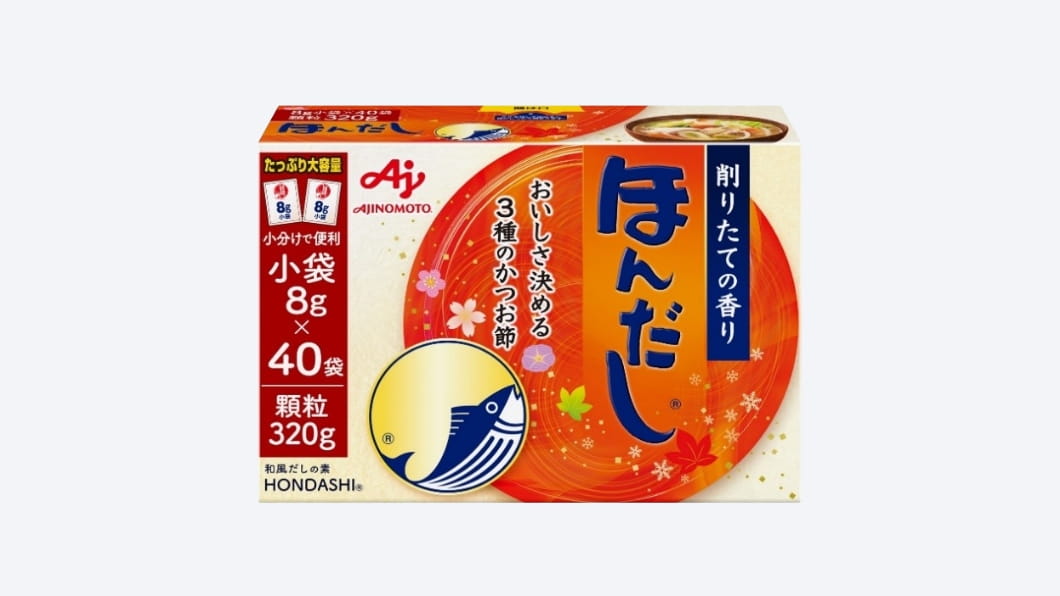
Photo Courtesy: Ajinomoto Co.
(Product name: "Hondashi")
Food containers and packaging play an important role in protecting the contents. We are constantly evolving polyethylene for food containers and packaging to make them easier to use; for example by making them easier to open, less wasteful; for example lengthening shelf life and reducing food wastes, and more environmentally friendly.
In recent years, the 3Rs (Reduce: reduce waste, Reuse: reuse, Recycle: recycle) are being strongly promoted to maintain the balance of environment and economic growth.
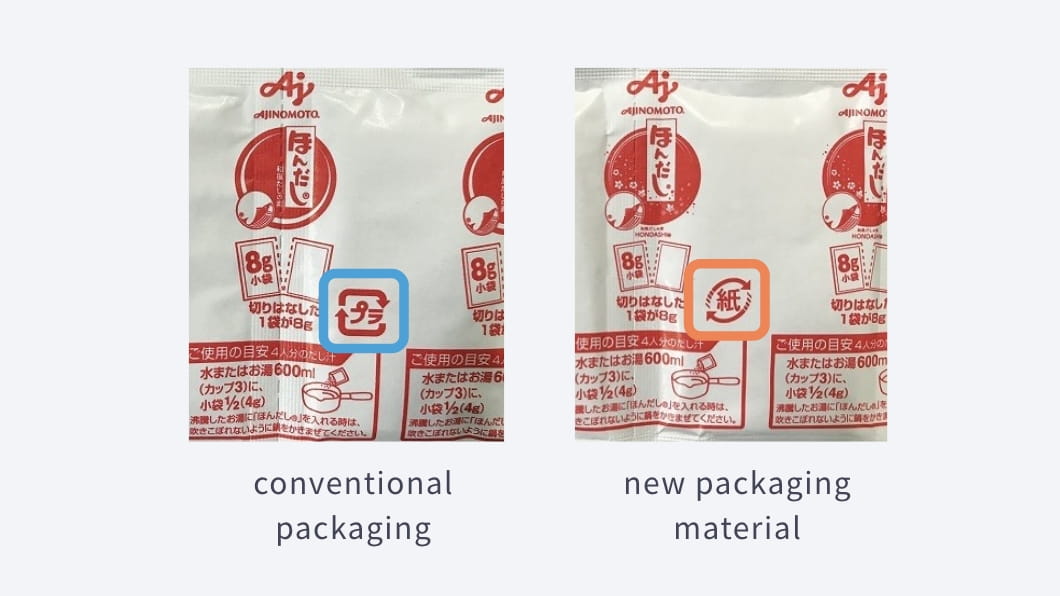
Identification mark labeling on packaging materials has been changed from “plastic” to “paper” because the resin layer thinned.
We are especially working on Reduce, which is one of the most important waste-related issues and are working to develop a grade which can thinner the packaging while maintaining the conventional package’s protectiveness and openability.
We will continue to provide products that contribute to the reduction of environmental impacts by making full use of the technologies we have cultivated.
Developing products using bio-polyethylene
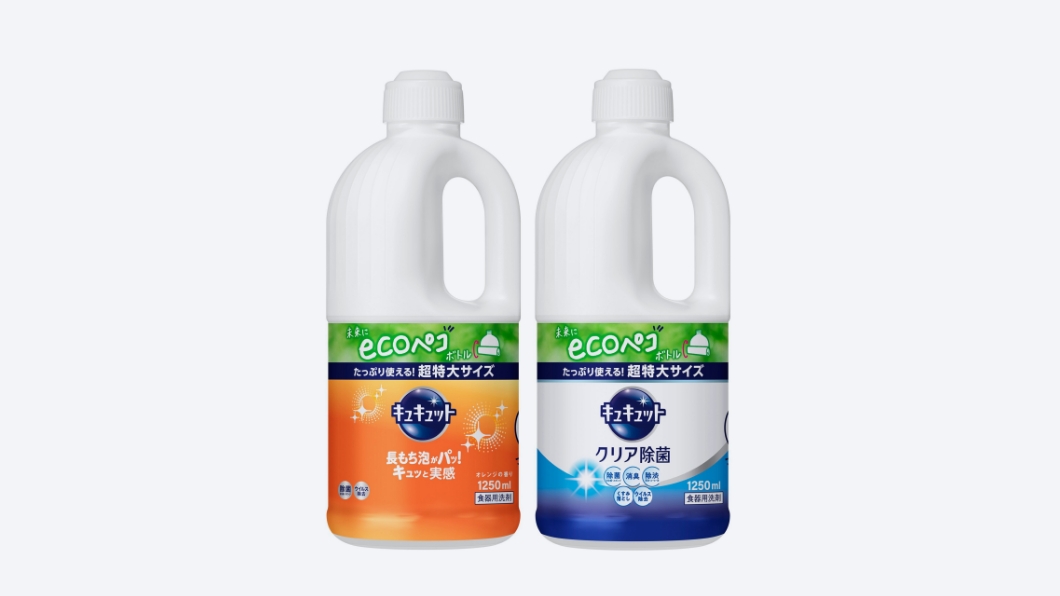
Kao Corporation, CuCute (1,250 ml)
Global warming has become a major social issue due to the increase of disasters associated with climate change. Therefore, amount of carbon dioxide, one of the greenhouse gases that cause global warming, needs to be reduced, and the using plant-derived materials are now being promoted as a countermeasure.
Polyethylene made from plants is an environmentally friendly plastic because the raw material plants absorb carbon dioxide from the atmosphere as they grow, and the impact they have on global warming throughout the product life cycle is relatively small. It can also contribute to reducing the consumption of finite fossil resources.
We have developed NOVATEC™ HD HB330EBP, which is made of biopolyethylene from plant-derived ethanol, and Kao Corporation has adopted it for the refill container of its dishwashing detergent, CuCute (1,250ml). NOVATEC™ HD HB330EBP is registered on the BiomassPla Positive List of the Japan BioPlastics Association as polyethylene with as a polyethylene with a biomass plastic content of 31%.
Developing compatibilizer for material recycling of PE/PA multilayer film
Polyethylene is widely used in food packaging materials and is often multilayered with EVOH or polyamide to provide barrier properties against oxygen and other substances. However, polyethylene and EVOH/polyamide do not mix well, and when you try to recycle these multilayer products, their transparency, appearance, and strength deteriorate. So, in many cases they are just disposed.
To solve these problems, we have developed a compatibilizer that improves the mixability of polyethylene with EVOH and polyamide. Adding this compatibilizer during recycling improves the dispersion of the barrier material. This improves the transparency of the film made by the recycled resin. It also improves various film properties such as tensile properties, impact resistance, and tear strength, making it possible to reuse the film as a practical film molding resin.
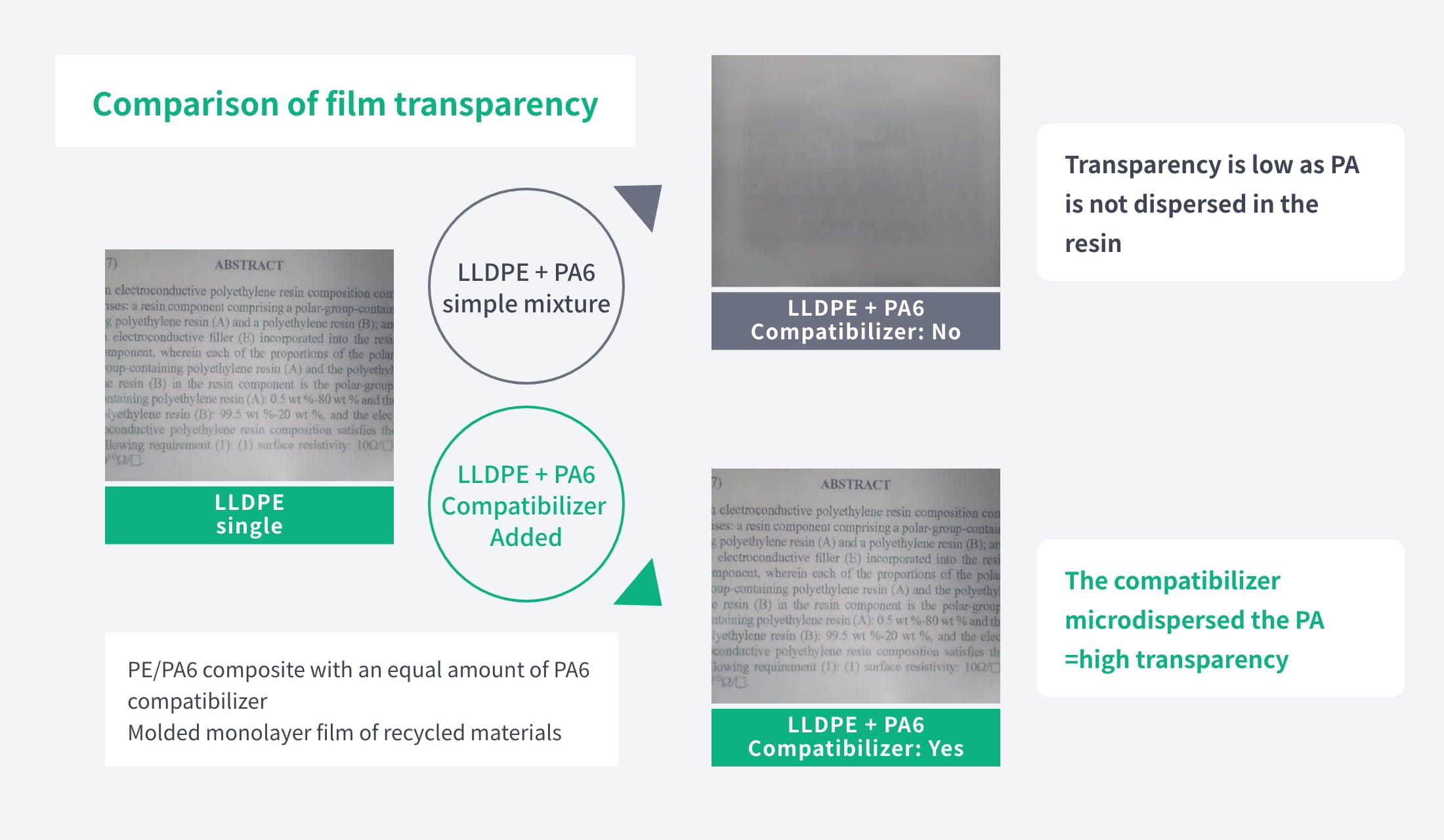